Reducing the complexity of multi storey construction - save money, save time and improve safety.
The jJack building system was developed in response to home owners and builders frustrations with the safety, time and cost issues of traditional multi storey construction. Traditionally work is performed on scaffolds using cranes and hoists to load materials onto upper levels. Ladders are required to provide access for people. These methods complicate the building process, are costly, reduce room and access on site, slow down work, cause delays and create a safety issue.

Scaffold restricts access on site
Delays associated with using scaffold arise from restricted room on site, blocking of access to the ground floor and working at heights.

Builders hoists can be dangerous
Tradespeople prefer to work at ground level. With more room on site and working at ground level multiple tasks can be done at the same time.

Construction work is easier at ground level
And working at heights has its dangers
By using the jJack system, visits to site by trades can be reduced up to 70%
To build a 2 storey home scaffold must be raised and lowered upto 3 times. This means trades must leave site and return after each scaffold change. Before adjusting scaffold it must be emptied, raised or lowered and re loaded before trades can return to work.
Working at ground level (without scaffold) means less visits to site and a lot less down time.
During boom times these delays are magnified are the cause of long delays due to trades having to leave site and start other jobs. This is a major cause of long build times and its not unusual for 2 storey homes to take upto 30 months to plan and complete. Eliminating the need for trades to leave site reduces delays.
Through a constant review process it was realised the majority of construction delays resulted from using scaffold, cranes and hoists.
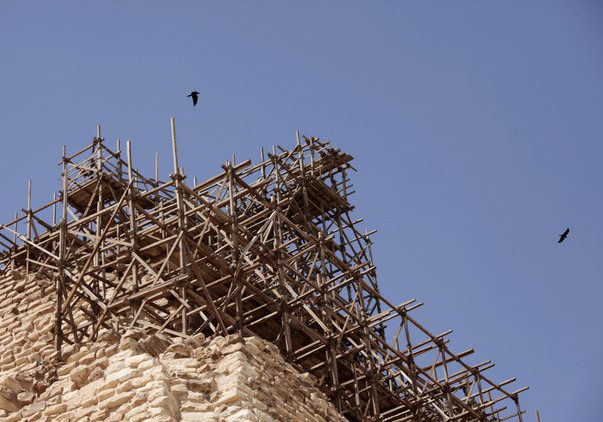
Scaffold is as ancient as the Pyramids
Changing this traditional method would be going against the well established status quo. Trades were well acquainted with working on scaffold and using cranes and hoists to lift materials onto the new levels above the ground floor.
The constant search for faster, better, less expensive building process and products lead to the latest development of The JJack Building system, building the upper floor at ground level and then jacking it up to build underneath.
The idea of eliminating scaffold attracted enthusiasm from builders and building trades who were frustrated with the dangers of working at heights, restricted access, less room available on site, having to leave site while scaffold was cleared, partly dismantled, lifted to a higher level, reloaded with materials before workers could return to site and then set up again to re start work.
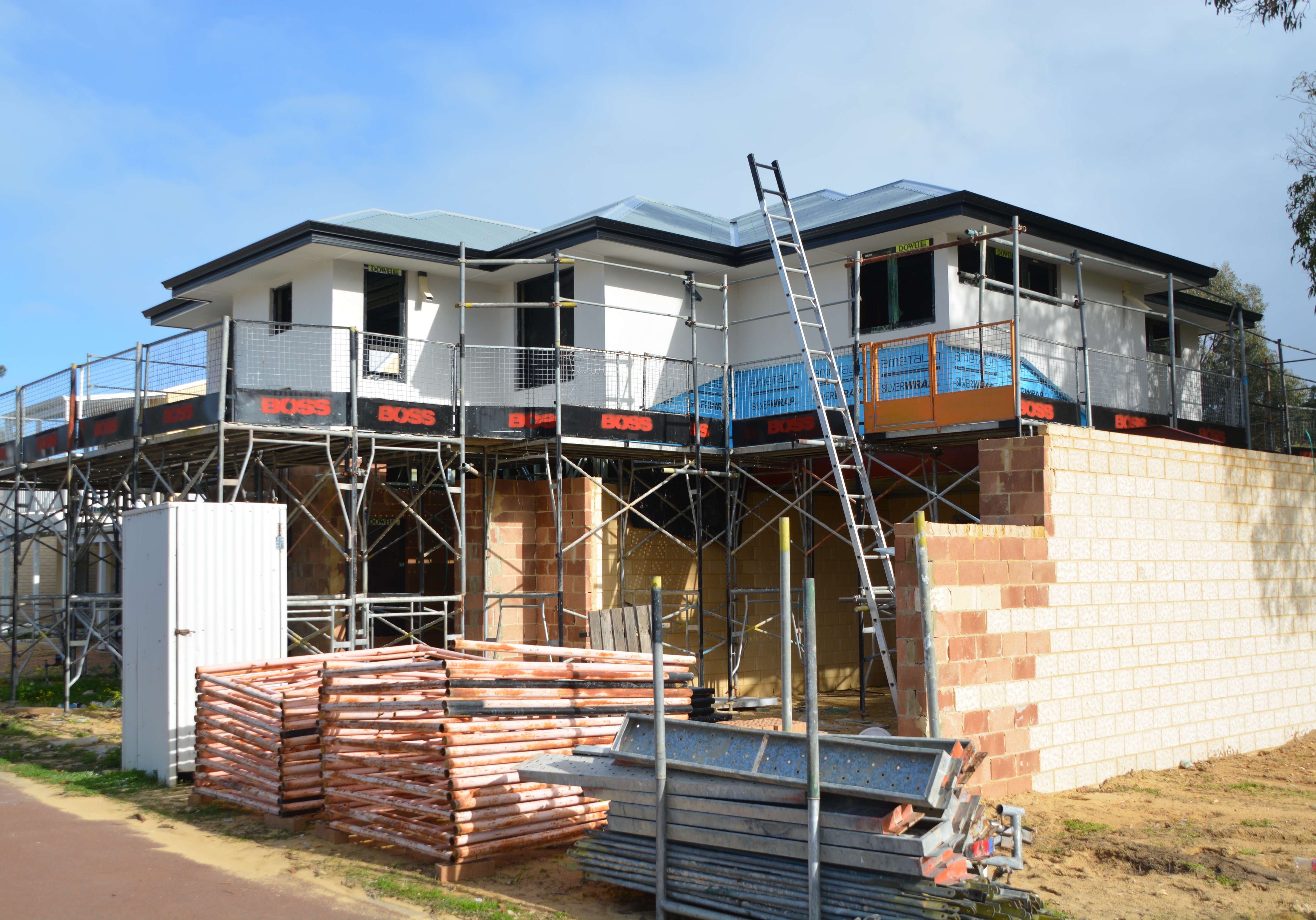
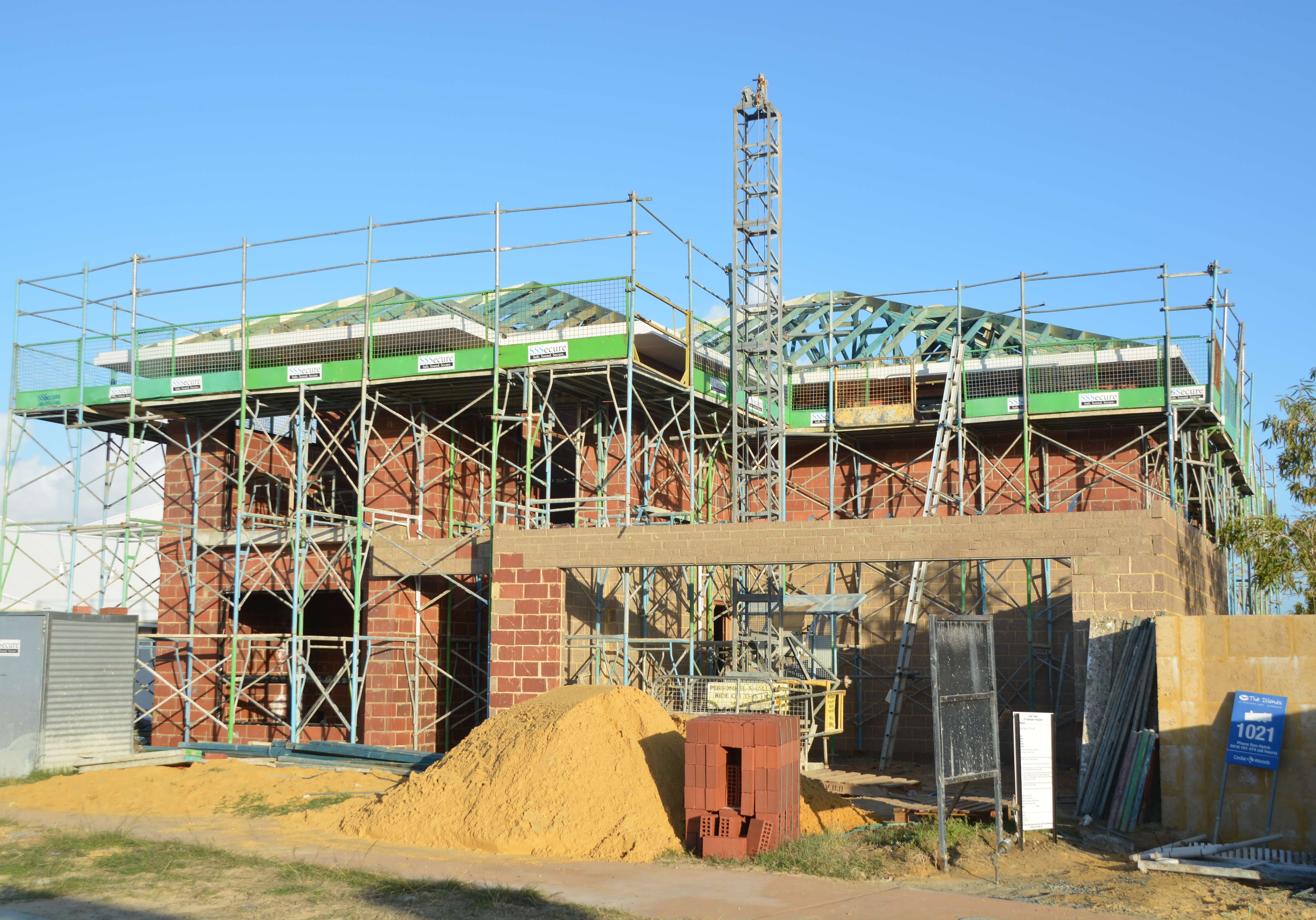
For builders this scaffold raising and lowering process resulted in delays & costs, resulted in working at height dangers and costs, caused delays with workers leaving site and returning after scaffold raising and reloading and often causes damage to finished surfaces. Consequently builders were enthusiastic about the idea of eliminating scaffold, cranes and hoists

Phil Jenner
Founder & CEO, jJack Systems
Philip Jenner is driving force behind the development of the jJack building system.
A registered builder, he started his building career in 1989 and founded Great Living Homes in 1992 specialising in the 2 storey market.
Phil's focus has always been on build quality, innovative design, reducing complexity and speed of construction. By 2009 the company was selling nearly 100 homes a year.